Case study
New-Era Corporation and LC Magna
Photocentric solutions have opened up new possibilities and markets for a company with 85 years of manufacturing history.
New-Era Corporation, founded in Tokyo in 1939 as a manufacturer of magnetic switches, introduced the LC Magna in 2023. The initial goal was to reduce in-house manufacturing costs and shorten delivery times.
However, as they continued using the LC Magna, they discovered its “strong suitability for customization,” which allowed them to expand into fields they had never previously imagined.
Our distribution partner in Japan, 3DPC, spoke with Izumi Keisuke, Executive Officer and Quality Assurance Manager at New-Era Corporation, and Muraoka Kimiki, Group Manager of the FA Unit in the Sales Department. They discussed the process that led to the introduction of the LC Magna and the company’s unexpected expansion into the medical field following its adoption.
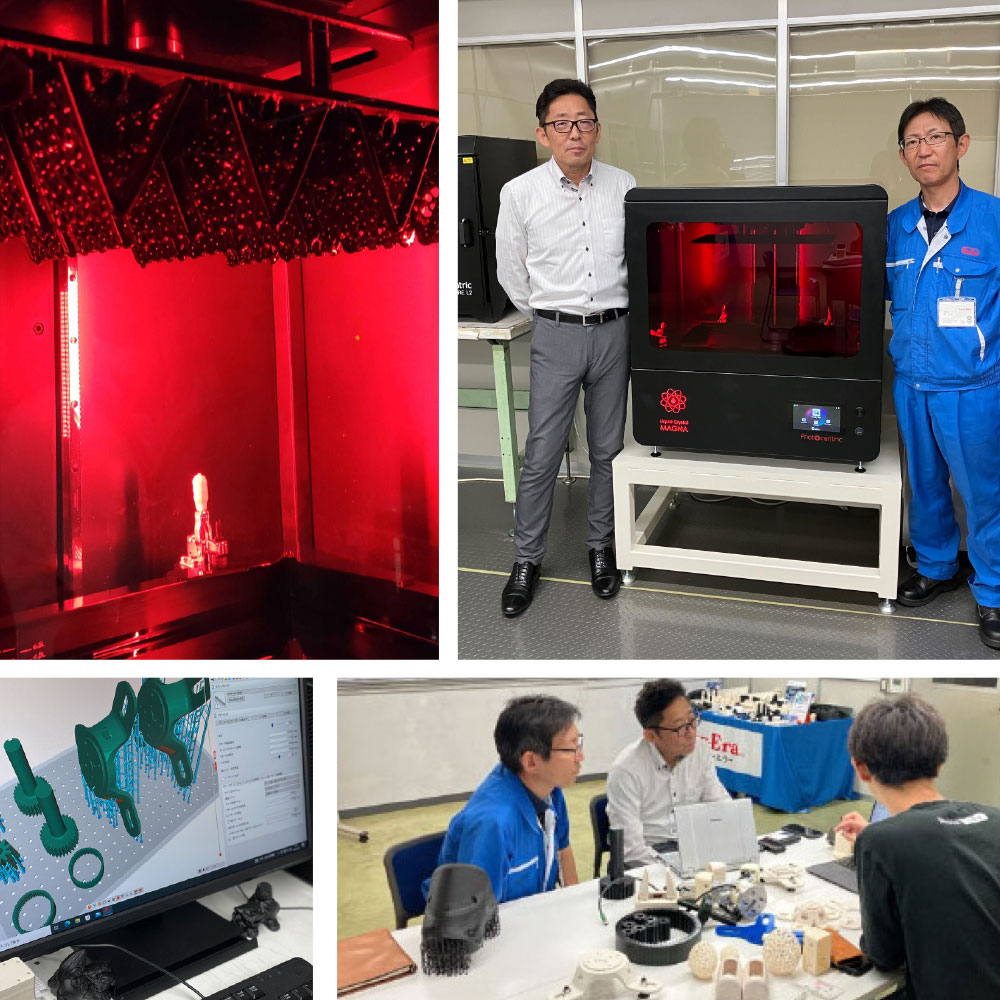
Background to the introduction of LC Magna and reasons for deciding to purchase it
What led you to introduce the LC Magna?
Izumi: There are two main reasons. First, our company has an electric gripper for a collaborative robot that works alongside people. From a risk assessment perspective, we needed to create a resin guard to protect people from protruding objects and other safety concerns. Initially, we considered cutting or inkjet printing, but inventory management would have been a hassle. With a 3D printer, we can produce parts on demand, so we decided to purchase one. For some products, we also offer a service that includes the customer’s company name or logo. This is only possible with a printer and allows us to meet specific customer requests.
Muraoka: The second benefit is using the printer as a key solution in our development department to produce prototypes for new products. Previously, we had to rely on third-party companies, which meant waiting a long time for prototypes. Now, with a 3D printer in-house, we can design and produce a prototype in just 10 to 20 hours. Holding the prototype in your hands gives a much better sense of the product. It’s also much easier to explain the concept to customers using a physical model rather than blueprints.
Introducing the LC Magna
3DPC: What were you hoping to achieve when you purchased the LC Magna?
Izumi: Cost savings were a significant factor. Prototyping is surprisingly expensive. With a 3D printer, after the initial setup, you can produce additional iterations at a fraction of the cost—just the material expense. However, the biggest advantage is time savings. Previously, it took about a month to create a blueprint, finalise and agree on a quote, and start production. Now, as soon as the blueprint is ready, we can start moulding immediately. Even if adjustments or rework are needed, the time saved on the first prototype makes the entire process faster. This is what people mean by “time is money.” Condensing the development timeline is a clear advantage.
With the LC Magna, we can also produce parts in one go. The large build area lets us print multiple parts simultaneously. With FDM printers, making parts one by one takes much longer. Additionally, in typical light-based resin curing processes, the resin is hardened layer by layer from the bottom up. Small general-purpose printers often face issues where the cured parts snap during detachment. The LC Magna eliminates this problem, allowing for the production of large objects seamlessly
“Cost savings were a significant factor. Prototyping is surprisingly expensive. With a 3D printer, after the initial setup, you can produce additional iterations at a fraction of the cost. Time is money”.
Izumi Keisuke
Executive Officer and Quality Assurance Manager
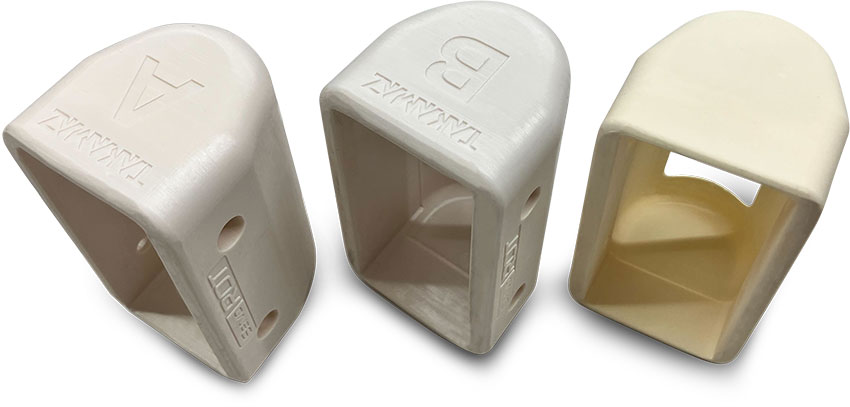
3D printed case with company name and logo
Reasons for choosing LC Magna and its ease of use
3DPC: What was the selection process like for choosing this equipment?
Izumi: Among the options—inkjet, light-based curing, and FDM—I wanted something capable of producing beautiful resin shapes. FDM can be frustrating because of the visible layer lines. When I tried inkjet and light-based curing as alternatives, I noticed that inkjet prints turned yellow under ultraviolet light. While inkjet offers fine detail, its colour stability is poor. By contrast, the LC Magna’s White Stencil material, with a resolution of 25 microns, performed very well. I’m happy I chose it because it lets me create a wide variety of objects.
3DPC: What did you think of the LC Magna’s operability and ease of use?
Izumi: Operating it is straightforward—just input the data and press the switch. The results closely match what I imagine. The software is very user-friendly, with features like automatic support placement. At first, I thought manually adding supports would be impossible, so the automation was helpful. Now that I’m more experienced, I sometimes make manual adjustments for specific results. For me, this balance works best.
“Previously, processing one part cost over 100,000 yen ($650+). With the LC Magna, the resin cost is only about 1,000 yen (~$6.50)”.
Izumi Keisuke
Executive Officer and Quality Assurance Manager
Reducing a Three-Month Process to 10 Hours
3DPC: What efficiency gains has this equipment provided over traditional manufacturing methods?
Izumi: Previously, processing one part cost over 100,000 yen ($650+). With the LC Magna, the resin cost is only about 1,000 yen (~$6.50). This has significantly reduced running costs. Additionally, what used to take one to three months now takes just 10 hours. For the first prototype, speed is more important than cost. The ability to create and touch the prototype immediately is the biggest benefit
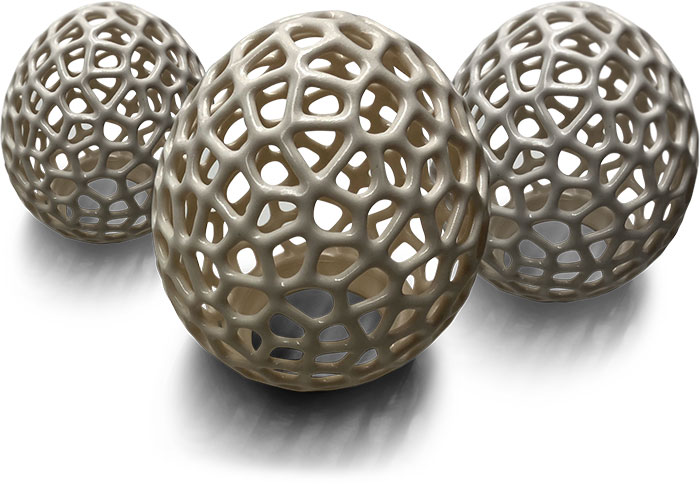
3D Printed parts on LC Magna
What can be made with LC Magna and with what precision?
3DPC: What products and parts are you currently building with the LC Magna?
Izumi: We primarily produce four components: the suction plate, hand cover, case, and wiring parts. For example, we attach suction plates to robots for testing. Metal cutting creates significant waste, but with a 3D printer, material waste is minimal. The printer allows us to produce custom shapes quickly to meet specific customer needs.
Muraoka: We design and handle everything from the shape of the jig for the workpiece to prototyping and production. If a customer provides us with STL data for a specific jaw shape, we can create that shape. While we are not a robot manufacturer, we hope to eventually combine robots and actuators into complete systems. Our goal is to evaluate the workpiece as a test and propose to customers that we can actually perform suction gripping.
We also provide cases that include the customer’s company name and logo. Additionally, we use the printer to create the main body of the wiring parts. Instead of just sharing 3D CAD data, it’s more effective to verify the wiring and details by handling the actual product. This approach helps solve issues that blueprints alone cannot address. For example, if a part is incorrect, we can quickly remake it. Outsourcing such a prototype would cost around 100,000 yen (approximately $650), but with the printer, it can be done in a day for just a few thousand yen (less than $20). This speed and cost-efficiency are highly appreciated.
3DPC: What about the quality and precision of the build?
Izumi: Of course, sink marks and bending are inevitable since it’s resin, but I think White Tensile and Dental White materials are surprisingly accurate compared to the modelling data. Our company primarily manufactures hard objects, but I’ve heard that the LC Magna can also produce soft objects like rubber, which I’d like to experiment with in the future.
“Outsourcing such a prototype would cost around 100,000 yen (approximately $650), but with the printer, it can be done in a day for just a few thousand yen (less than $20)”.
Muraoka
Executive Officer and Quality Assurance Manager
3DPC: What advice or experiences would you like to share with other companies or industries considering introducing the LC Magna?
Izumi: One of its greatest strengths is its ability to create large models. Based on my experience, the software provides automatic support, making it user-friendly even for beginners. I can create many models, and I’m satisfied with the modelling area size. Since it’s a printer made by a British company, I initially worried about what kind of support I would receive if there were any issues. However, with 3DPC acting as an intermediary, I feel reassured. They don’t leave you on your own—they truly look after you (laughs). When I encountered some initial problems with the printer, they provided excellent support, allowing me to use it with confidence.
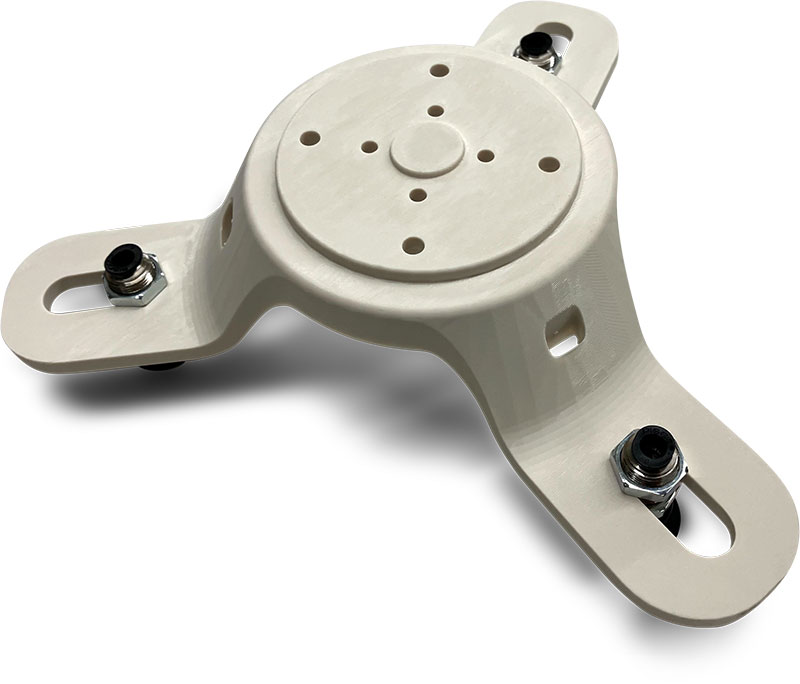
Adsorption plate
Expanding into the medical field, something we never imagined
3DPC: What new products or projects have been made possible by introducing the LC Magna?
Izumi: The medical field requires high levels of customisation and cannot rely on mass production. Each product must be tailored to fit an individual. This is where the LC Magna has a major advantage—it can quickly create customised shapes for each person. Instead of limiting ourselves to the machine’s specifications, we started exploring how we could apply its capabilities to meet new needs.
3DPC: What directions, improvements, or business prospects do you foresee for the future use of LC Magna?
Muraoka: I can’t go into the details, but we’re collaborating with a university to develop products for medical environments and nursing care facilities using 3D printers. Before introducing the LC Magna, I had no interest in the medical field. Now that I’ve seen how well the LC Magna handles customization, I want to expand into this area.
Ultimately, I would like to be able to make in-house. Currently, we still outsource production to processing companies, but my vision is for us to handle everything—from design to manufacturing—on our own.
Original article: https://www.3dpc.co.jp/articles/photocentric-newera-interview
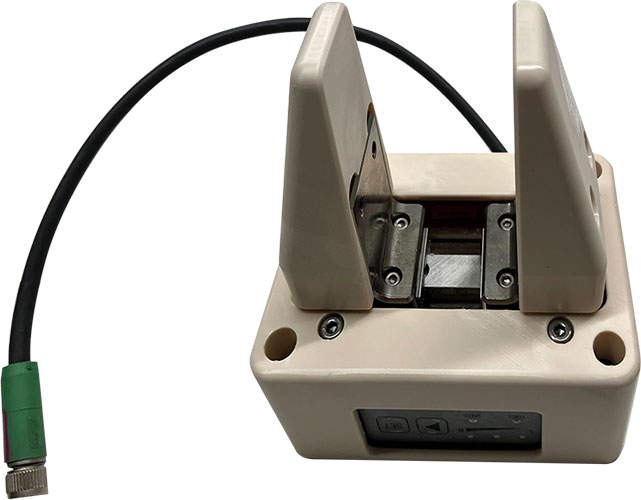
Electric actuator with guard
Expanding into the medical field, something we never imagined
3DPC: What new products or projects have been made possible by introducing the LC Magna?
Izumi: The medical field requires high levels of customisation and cannot rely on mass production. Each product must be tailored to fit an individual. This is where the LC Magna has a major advantage—it can quickly create customised shapes for each person. Instead of limiting ourselves to the machine’s specifications, we started exploring how we could apply its capabilities to meet new needs.
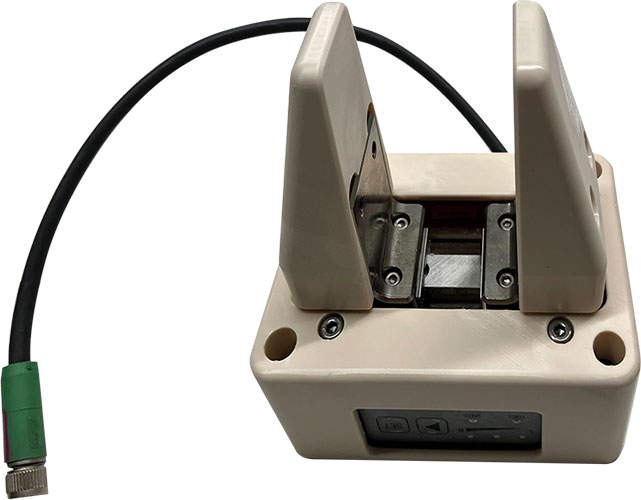
Electric actuator with guard
3DPC: What directions, improvements, or business prospects do you foresee for the future use of LC Magna?
Muraoka: I can’t go into the details, but we’re collaborating with a university to develop products for medical environments and nursing care facilities using 3D printers. Before introducing the LC Magna, I had no interest in the medical field. Now that I’ve seen how well the LC Magna handles customization, I want to expand into this area.
Ultimately, I would like to be able to make in-house. Currently, we still outsource production to processing companies, but my vision is for us to handle everything—from design to manufacturing—on our own.
Original article: https://www.3dpc.co.jp/articles/photocentric-newera-interview