3D printing solutions
Automotive Aftermarket
We supply resins that create printed parts that look and perform like tooled plastic. The cost-effective alternative, proven in real-life applications, used in all weather conditions.
Titan creates large dimensionally accurate pieces for numerous auto applications, such as panels and covers.
Magna is proven as the most effective method of making small and medium sized fixtures for the automotive aftermarket sector. It has created hundreds of thousands of parts for companies typically where they have a lot of designs with low to medium volumes that don’t merit tooling.
For large volumes of functional parts, there is only one solution, Magna.
3D printing solutions
Automotive Aftermarket
Magna is proven as the most effective method of making small and medium sized fixtures for the automotive aftermarket sector. It has created hundreds of thousands of parts for companies typically where they have a lot of designs with low to medium volumes that don’t merit tooling.
We supply resins that create printed parts that look and perform like tooled plastic. The cost-effective alternative, proven in real-life applications, used in all weather conditions.
Titan creates large dimensionally accurate pieces for numerous auto applications, such as panels and covers.
For large volumes of functional parts, there is only one solution, Magna.
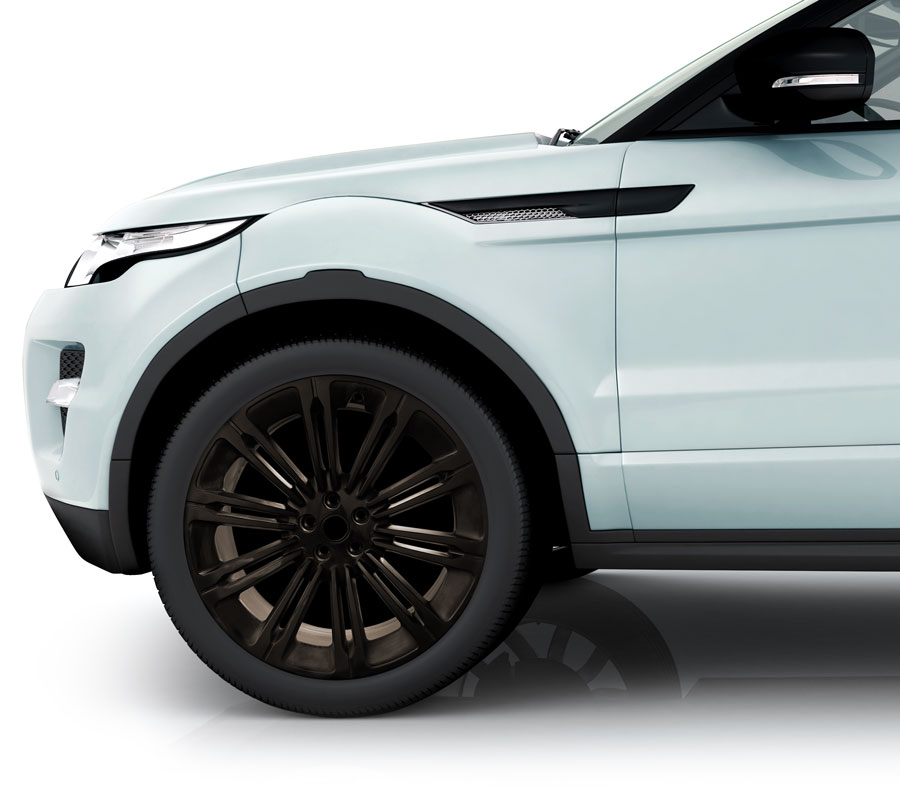
Printing large complex automotive panels for Magna International
Magna International needed 10 large containers to hold electrical components for test vehicles. 3D printing was the only option, but large format laser SLA was too expensive, too slow and the parts wouldn’t be functional in use. This is the story of some of the largest parts to be printed free radically, accurate in the z axis at +/- 0.065% average, printed on Liquid Crystal Titan.
LUMotorsport
Since 2003, LUMotorsport has represented Loughborough University at Formula Student events worldwide. The primary event is Formula Student UK, held at Silverstone each year. Last year 60 + teams from the UK and around the world competed. The team has also competed in Austria, Czechia, Germany and Hungary.
In 2023, LUMotorsport approached Photocentric to utilise their expertise in 3D printing. Working together, they have printed multiple aerodynamic parts, composite tooling and motorsport-standard electrical junction boxes for this year’s car, using the Liquid Crystal Magna 3D printer offering the following:
- Large-scale parts
- Complex, non-planar geometry
- Large height to bed contact area ratio
- Clean surface finish to minimise skin friction
- Increased design freedom for carbon tooling without the constraints of machining tooling block
- Lower weight inserts for aerodynamic surfaces compared to previous aluminium ones
LUMotorsport
Since 2003, LUMotorsport has represented Loughborough University at Formula Student events worldwide. The primary event is Formula Student UK, held at Silverstone each year. Last year 60 + teams from the UK and around the world competed. The team has also competed in Austria, Czechia, Germany and Hungary.
In 2023, LUMotorsport approached Photocentric to utilise their expertise in 3D printing. Working together, they have printed multiple aerodynamic parts, composite tooling and motorsport-standard electrical junction boxes for this year’s car, using the Liquid Crystal Magna 3D printer offering the following:
- Large-scale parts
- Complex, non-planar geometry
- Large height to bed contact area ratio
- Clean surface finish to minimise skin friction
- Increased design freedom for carbon tooling without the constraints of machining tooling block
- Lower weight inserts for aerodynamic surfaces compared to previous aluminium ones
Hymer Caravan Panel
Printing large scale prototype parts
The VisionVenture, co-created by BASF and HYMER, is a near-production glimpse into the future of van life. Body panels for the prototype were printed using the Liquid Crystal Titan printer.
Hymer Caravan Panel
Printing large scale prototype parts
The VisionVenture, co-created by BASF and HYMER, is a near-production glimpse into the future of van life. Body panels for the prototype were printed using the Liquid Crystal Titan printer.
Hymer Panel
Print Details:
Printer: Liquid Crystal Titan
Dimensions: 920 (W) x 470 (H) x 600mm (L)
Print Time: 40 hours
Resolution: 100µm
Resin Volume: 800g
Resin: Daylight Hard Black
Unit Cost: €48.96
Step 1 – Designing for Additive
Although the design supplied by Magna International had taken into account guidelines for AM, design optimization was still needed. The original design would have warped in production but Photocentric was given design freedom on the non-facing surfaces given that we met the external dimensions and were within tolerance on a total of 18 critical measurements. A gyroid infill was added with a 1.2mm by 12mm structure. A design correction for shrinkage of 0.5% in x:y and 0.1% in z was applied to achieve tolerance.
Step 2 – Supporting to achieve part tolerance
The part was orientated at an angle of 60 degrees to negate any sudden changes in force while printing. The support network was generated from the auto support function on Voxel Dance software for Photocentric. Support density was reduced to the minimum necessary to reduce support resin and work in sanding artefacts. Support tips were optimized at 0.6mm to deliver compromise between meeting the minimum level of physical restraint for the part and ease of support removal.
Cut out shapes will distort as the forces change when the open panel is reached. For dimensional accuracy in cut out shapes, you can insert supports or, easier is to insert thin 3mm blanking plates with a few attachment points.
Step 3 – Printing
The material property requirement for the enclosure was met by BASF EPD2006 resin.
The supported file was loaded onto a Liquid Crystal Titan.
The file was printed in 100my layers, taking 68 hours (7223 layers). The part weighed 4591g with 2062g of supports.
Step 4 – Wash process
By the end of the print, the platform had dripped free from excess resin, returning it to the tank. The platform was transferred via the Photocentric platform transfer to the Photocentric Wash XL unit. The door was locked, and the wash pump engaged, and the platform set to continuous rotation. The operator used the wash wand to spray a recirculating solution of Photocentric Resin Cleaner 30 into all areas of the part. Full cleaning took 15 minutes. At the end of the wash cycle, the sump of cleaning fluid was drained back to the IBC of wash fluid and the pump was switched to rinse. The part was rinsed with water to remove all remaining cleaning fluid for 5 mins. As remaining water can leave white marks on the parts, the air wand was applied for a couple of minutes.
Step 5 – Cure process
The platform transfer was then used to move the platform to the Photocentric Cure XL. The platform was rotated continuously to ensure even cure. It was fully post-processed with a combination of dual wavelength (405nm and 460nm) high intensity light and 60°C heat for a total of 5 hours.
Step 6 – Support removal
The fine Voxel Dance support tips were easily ripped off the part leaving minor raised artefacts which were then sanded. Total support removal time was 15 mins.
Step 7 – Adding inserts
We chose to sand the part further for approx. 120 mins, using an orbital sander, in order to get the best surface finish. The required inserts were hammered into the recesses. It was spray painted, with a primer and black coat.
Step 8 – Iterative learning
If you have made a similar type of part before, you will know how accurate the part is to CAD. If you are printing a new complex geometry, there may be variances from tolerance or defects, these are measured and then iteratively improved.
Step 1 – Designing for Additive
Although the design supplied by Magna International had taken into account guidelines for AM, design optimization was still needed. The original design would have warped in production but Photocentric was given design freedom on the non-facing surfaces given that we met the external dimensions and were within tolerance on a total of 18 critical measurements. A gyroid infill was added with a 1.2mm by 12mm structure. A design correction for shrinkage of 0.5% in x:y and 0.1% in z was applied to achieve tolerance.
Step 2 – Supporting to achieve part tolerance
The part was orientated at an angle of 60 degrees to negate any sudden changes in force while printing. The support network was generated from the auto support function on Voxel Dance software for Photocentric. Support density was reduced to the minimum necessary to reduce support resin and work in sanding artefacts. Support tips were optimized at 0.6mm to deliver compromise between meeting the minimum level of physical restraint for the part and ease of support removal.
Cut out shapes will distort as the forces change when the open panel is reached. For dimensional accuracy in cut out shapes, you can insert supports or, easier is to insert thin 3mm blanking plates with a few attachment points.
Step 3 – Printing
The material property requirement for the enclosure was met by BASF EPD2006 resin.
The supported file was loaded onto a Liquid Crystal Titan.
The file was printed in 100my layers, taking 68 hours (7223 layers). The part weighed 4591g with 2062g of supports.
Step 4 – Wash process
By the end of the print, the platform had dripped free from excess resin, returning it to the tank. The platform was transferred via the Photocentric platform transfer to the Photocentric Wash XL unit. The door was locked, and the wash pump engaged, and the platform set to continuous rotation. The operator used the wash wand to spray a recirculating solution of Photocentric Resin Cleaner 30 into all areas of the part. Full cleaning took 15 minutes. At the end of the wash cycle, the sump of cleaning fluid was drained back to the IBC of wash fluid and the pump was switched to rinse. The part was rinsed with water to remove all remaining cleaning fluid for 5 mins. As remaining water can leave white marks on the parts, the air wand was applied for a couple of minutes.
Step 5 – Cure process
The platform transfer was then used to move the platform to the Photocentric Cure XL. The platform was rotated continuously to ensure even cure. It was fully post-processed with a combination of dual wavelength (405nm and 460nm) high intensity light and 60°C heat for a total of 5 hours.
Step 6 – Support removal
The fine Voxel Dance support tips were easily ripped off the part leaving minor raised artefacts which were then sanded. Total support removal time was 15 mins.
Step 7 – Adding inserts
We chose to sand the part further for approx. 120 mins, using an orbital sander, in order to get the best surface finish. The required inserts were hammered into the recesses. It was spray painted, with a primer and black coat.
Step 8 – Iterative learning
If you have made a similar type of part before, you will know how accurate the part is to CAD. If you are printing a new complex geometry, there may be variances from tolerance or defects, these are measured and then iteratively improved.