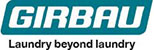
Case study
Adapt and Innovate with 3D Printing
Intro and application:
As a manufacturer of equipment for laundry services, Girbau sought to improve the efficiency of their folding machines. In realising that the air flow of their folding machine was not optimal for the precision folding they needed, Girbau turned to 3D printing for the speed, efficiency, limitless design possibilities, and cost-effectiveness of this technology to create the single solution part they needed to optimise their folding machines.
Challenges:
1. Redesigning of a part within a folding machine while still maintaining a competitive price point.
2. Using a material that is strong enough to create small cavities within the part to withstand high pressure.
Solution:
Optimising internal geometry for better performances
With the optimisation of the inner geometries of the part, the quantity of pressured air required to fulfill its function was reduced from 5.5 bars to 4 bars which resulted in lower air consumption and a more sustainable machine. The small channels created within the part to direct airflow significantly reduced the noise impact the machine makes. Previously with the basic drilled tube part, the airflow did not have a precise direction and the single tunnel echoed the sound of the air pressure.
Better design at a competitive price
During their additive design process, Girbau was able to design a part with complex geometries, integrated functional parts and lightweight and compact. The additive nature of 3D printing technology means that creating a complex part does not come at a higher price and in fact can be sometimes cheaper since less material is used. With these design possibilities, Girbau was able to create a single solution part that was cost-effective. This would not have been possible with traditional manufacturing methods since the design possibilities for traditional manufacturing require expensive moulds and large production volumes to make up for the cost.
Making the most of intergrated functions
The simplification of their part which now had integrated functions such as supports that made it possible to easily attach their part to a rack within the folding machine. A more compact model that would not be possible to find in the market or challenging to create with traditional manufacturing methods.

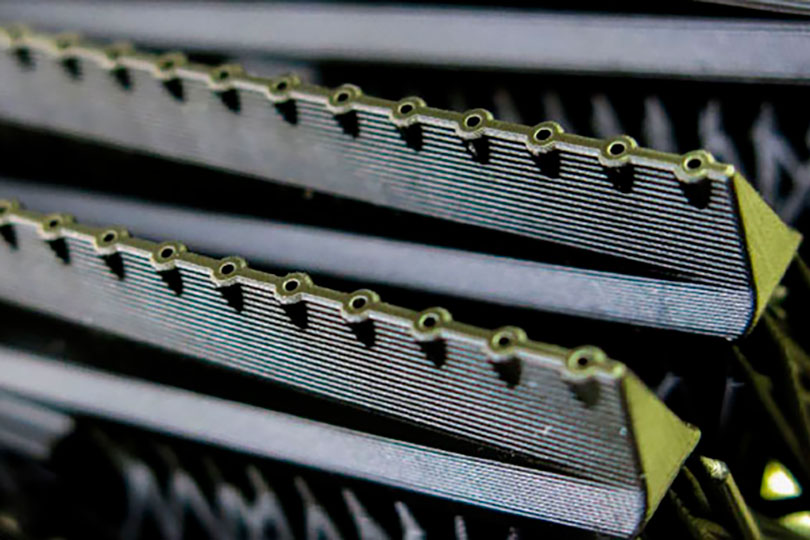
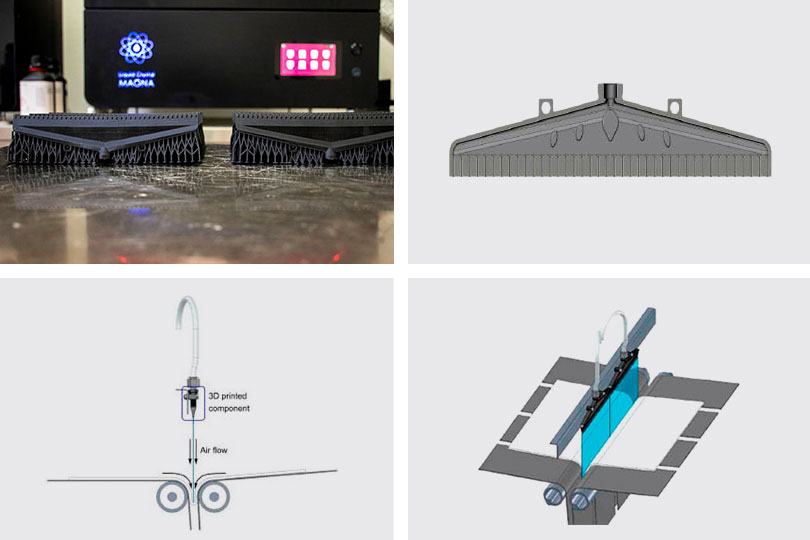

Sylvian Ferris, R&D Designer, Girbau
“Sculpteo’s experts supported us throughout the printing process so we could go on and print the model with the best solution to match our challenges.”
Ultracur3D® EPD 1006 & LC Magna : The precision needed to meet manufacturing challenges
With a final design, Girbau turned to Sculpteo’s online printing service to create a prototype that would potentially be the final part for their machines. They decided on SLS (selective laser sintering) technology and Nylon PA12 material. When testing the part, they realised that there was excess powder from the PA12 material blocking the airflow. With Sculpteo’s responsive customer support, Girbau was advised to use LCD (Liquid Crystal Display) printing technology to create tiny channels within the part, which powder technology cannot do, using the resin material EPD 1006. Parts printed with resin materials have high accuracy and are perfect for designs that require high precision, like Girbau’s part.
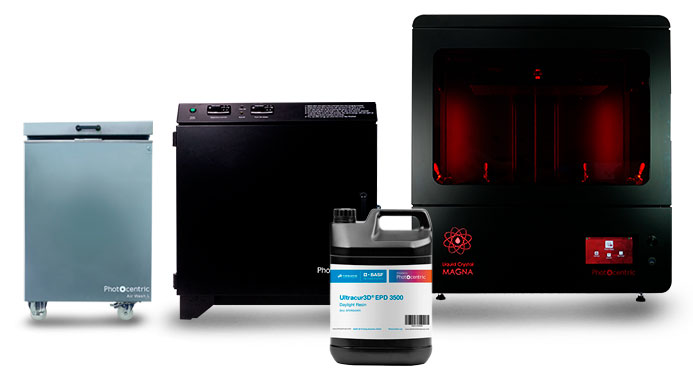
Equipment List:
Liquid Crystal Magna, Photocentric Air Wash L, Photocentric Cure L2, Ultracur3D® EPD 1006
Explore more case studies
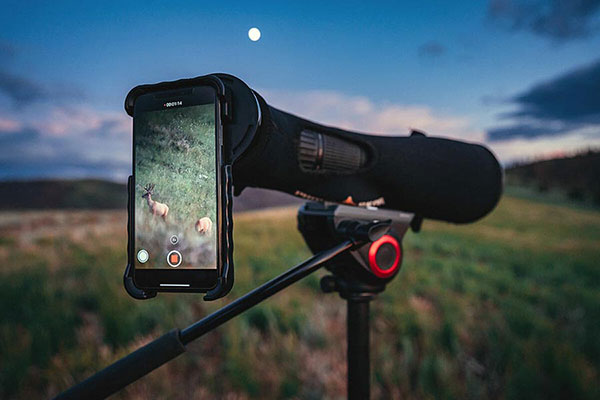
Phone Skope
Digiscoping leader
Phone Skope is a US manufacturer of precision engineered adaptors for almost any smartphone and has adopted the Liquid Crystal Magna as the solution to making lots of its custom-moulded digiscoping adaptors
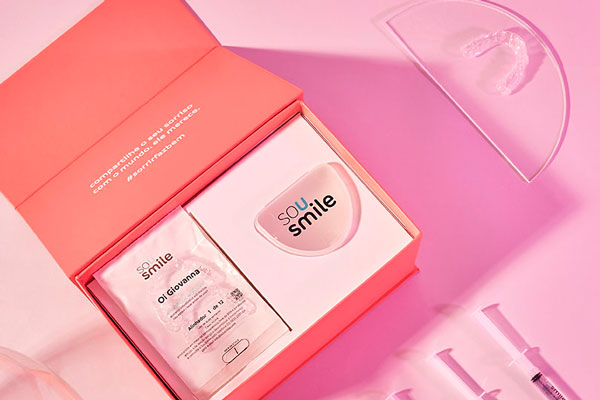
SouSmile
Aligner manufacturer
SouSmile is Brazil’s largest direct to consumer invisible aligner company with a presence in 30 cities, they invested in a trio of Photocentric Liquid Crystal Magna 3D printers to produce their dental aligners in scale.
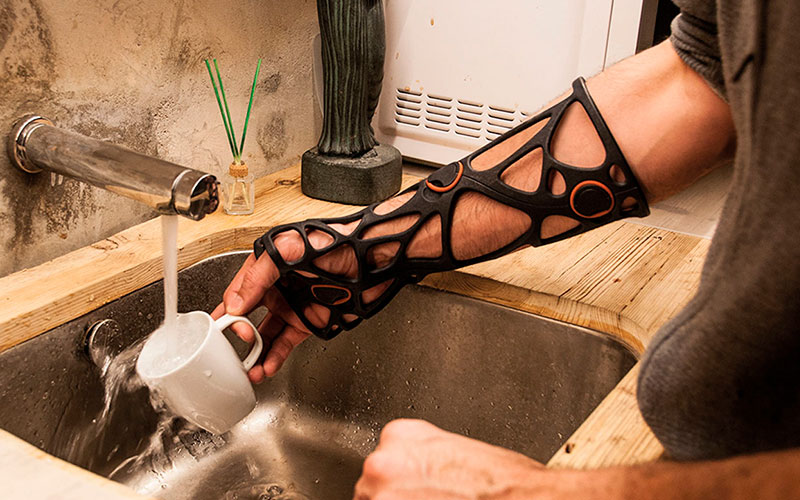
Xkelet
Orthotic manufacturer
The powerful alliance of Xkelet and Photocentric has seen the creation of an advanced solution to traditional orthotics; one which is revolutionising the treatment of damaged bones.