Our unique patented 3D LCD printing technology
Inventors of LCD 3D printing
LCD driven 3D printers have been the most significant invention in Additive Manufacturing in the last 7 years and have become the go to choice for high resolution, low price printing.
What is 3D printing?
3D printing or Additive Manufacturing allows 3D printed objects to be built up in successive layers until the desired shape is formed.
The individual layers are finely sliced cross sections of the overall object, and complex shapes can be created with freedom of geometry.
3D printing is now evolving from prototyping to mass manufacturing.
To appreciate the benefits of our patented LCD print technology we have summarised the differences between it and other stereolithographic (SLA) or vat polymerisation 3D printing methods
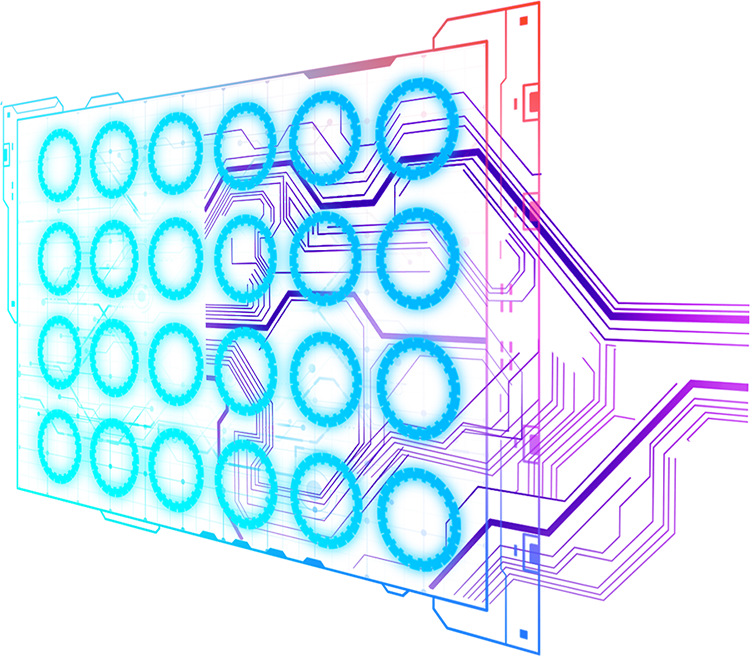
DLP
DLP projectors became a widely used alternative to lasers being able to cure a much larger area the size of a mobile phone screen at 2k and 4K resolutions. The bulb and Digital Mirror Device need replacing and calibrating. Even though it can cure an area larger than a laser beam, it cant match an LCD for resolution, reliability or cost.
Laser
The laser beam cures liquid photopolymer resin at very high resolution. However, because of the necessity to create each part voxel by voxel this is a time-consuming process. The laser and its galvanometer require regular calibration and replacement.
LCD
The concept we invented. Using an LCD screen as a light source, an entire layer is encoded simultaneously, rather than small area by area. LCD printing benefits from one of the greatest technological advances of the last 50 years the use of visual display screens. It can produce much larger volumes than alternative methods, creating new products at rates previously unimaginable. The simplicity of the process is its strength, if using daylight as opposed to UV, the exposure is even and the machine stable for many years of use.
Our unique patented 3D LCD printing technology
Inventors of LCD 3D printing
LCD driven 3D printers have been the most significant invention in Additive Manufacturing in the last 7 years and have become the go to choice for high resolution, low price printing.
What is 3D printing?
3D printing or Additive Manufacturing allows 3D printed objects to be built up in successive layers until the desired shape is formed.
The individual layers are finely sliced cross sections of the overall object, and complex shapes can be created with freedom of geometry.
3D printing is now evolving from prototyping to mass manufacturing.
To appreciate the benefits of our patented LCD print technology we have summarised the differences between it and other stereolithographic (SLA) or vat polymerisation 3D printing methods
DLP
DLP projectors became a widely used alternative to lasers being able to cure a much larger area the size of a mobile phone screen at 2k and 4K resolutions. The bulb and Digital Mirror Device need replacing and calibrating. Even though it can cure an area larger than a laser beam, it cant match an LCD for resolution, reliability or cost.
Laser
The laser beam cures liquid photopolymer resin at very high resolution. However, because of the necessity to create each part voxel by voxel this is a time-consuming process. The laser and its galvanometer require regular calibration and replacement.
LCD
The concept we invented. Using an LCD screen as a light source, an entire layer is encoded simultaneously, rather than small area by area. LCD printing benefits from one of the greatest technological advances of the last 50 years the use of visual display screens. It can produce much larger volumes than alternative methods, creating new products at rates previously unimaginable. The simplicity of the process is its strength, if using daylight as opposed to UV, the exposure is even and the machine stable for many years of use.
Masters of light
With our earliest granted visible light patent using LCD screens stretching back to Jan 2005 and 22 granted patents and a further 20 pending all concerned in innovations in 3D printing using LCD screens, we are the undisputed innovators in both LCD 3D printing and visible light polymerisation.
We use both daylight and UV in our LCD screen printers, but we prefer using visible light as the rate of cure through depth is more even and the screen suffers no light degradation, so in practice the printer can last a lifetime.
It is also much more effective to use daylight with dark pigment or particle rich formulations as the longer wavelength travels further through them than UV.
Masters of light
With our earliest granted visible light patent using LCD screens stretching back to Jan 2005 and 22 granted patents and a further 20 pending all concerned in innovations in 3D printing using LCD screens, we are the undisputed innovators in both LCD 3D printing and visible light polymerisation.
We use both daylight and UV in our LCD screen printers, but we prefer using visible light as the rate of cure through depth is more even and the screen suffers no light degradation, so in practice the printer can last a lifetime.
It is also much more effective to use daylight with dark pigment or particle rich formulations as the longer wavelength travels further through them than UV.
Daylight LCD printing explained
1) LED created the light source
Our printers use an array of LEDs as a light source, shining near parallel highly collimated light through the LCD panel and onto the resin layer. As an entire layer is exposed simultaneously it is highly efficient.
2) Sliced image is displayed on screen
The LCD screen is a black and white matrix that lets the light enter where it can cure polymer to make each layer of the finished part.
3) Daylight resin hardens
Our daylight resin is contained in a vat which hardens into functional plastic when selectively exposed to light.
4) Printing layer by layer
Photocentric printers create product using a “bottom-up” process, where the object being printed is pulled up layer by layer attached to the print platform, rising out of the resin bath. The process is repeated until the object is built.
Daylight LCD printing explained
1) LED created the light source
Our printers use an array of LEDs as a light source, shining near parallel highly collimated light through the LCD panel and onto the resin layer. As an entire layer is exposed simultaneously it is highly efficient.
2) Sliced image is displayed on screen
The LCD screen is a black and white matrix that lets the light enter where it can cure polymer to make each layer of the finished part.
3) Daylight resin hardens
Our daylight resin is contained in a vat which hardens into functional plastic when selectively exposed to light.
4) Printing layer by layer
Photocentric printers create product using a “bottom-up” process, where the object being printed is pulled up layer by layer attached to the print platform, rising out of the resin bath. The process is repeated until the object is built.
Advantages of LCD 3D printers
Accuracy
Prints can meet all other methods in resolution by using screens from VR headsets, mobiles, tablets, up to TV screens.
Faster printing
LCD printing creates more volume more quickly than other methods as complete layers are printed simultaneously.
Cost effective
LCD screens are the most cost effective and reliable visual display device on the planet which is constantly improving in resolution and lowering in price.
Reliability
LCD screens when exposed with daylight, the light intended to be emitted through them, can last a lifetime, think of how often you replace your TV.
Simplicity
It is very simple, illuminate the image and the screen does the work, its simplicity is its elegance and its power.
Blow-Peel Technology
The machine that breathes
We have invented a highly reliable and effective form of pressure relief mechanism. At the time of platform lift we insert air under the vat to enable the release to start at the perimeter of the cured object transferring in towards the centre, rather than as a solid area pulling away, ensuring no damage is imparted onto the object, we called it blow-peel.
It allows our customers to enjoy print reliability, regardless of the shape they are creating.
Vat-lift technology
We have invented a mechanism to remove peel force where the vat lifts before the platform does. This allows the part to peel away from the base of the vat from the back forwards, transferring the disruptive force from an area to a line.
It is highly effective and reliable and is used on our Liquid Crystal Opus printer. It allows our customers to enjoy maximum print performance reliability regardless of the shape being created.
1) Printed layer begins to form.
2) Vat lifts while platform is going up, separating the vat film from the LCD.
3) Vat returns to its original position, ready for the next layer.
Evolution of our 3D printers
Printer name
Year released
LCD screen
Build volume
1) LC10*
2) LCHR*
3) LC Precision*
4) LC Pro*
5) LC HR2*
6) LC Precision 1.5 *
7) LC Magna
8) LC Dental*
9) LC Opus*
10) LC Titan
11) JENI
2016
2017
2017
2017
2018
2018
2019
2020
2021
2024
TBC
10″- 1920 x 1080 px
9.7”- 2048 × 1536 px
5.5″- 1440 x 2560 px
23.8”- 3840 × 2160 px
9.7”- 2048 x 1536 px
5.5″- 2560 x 1440 px**
23.8″- 3840 x 2160 px**
14″- 3840 x 2160 px**
14″- 3840 x 2160 px**
32″ – 8K 7680 x 4320 px**
Configurable based on requirements
200 x 100 x 200 mm
196 x 147 x 250 mm
123 x 69 x 160 mm
470 x 240 x 340 mm
196 x 147 x 250 mm
121 x 68 x 160 mm
510 x 280 x 350 mm
310 x 174 x 200 mm
310 x 174 x 220 mm
695 x 385 x 1200 mm
Configurable (w) x 800 (d) x 2440 (h) mm
*Printer no longer on sale
**Backlit screen technology introduced
Evolution of our 3D printers
Printer name | Year released | LCD screen | Build volume
1) LC10* | 2016 | 10″- 1920 x 1080 px | 200 x 100 x 200 mm
2) LCHR* | 2017 | 9.7”- 2048 × 1536 px | 196 x 147 x 250 mm
3) LC Precision* | 2017 | 5.5″- 1440 x 2560 px | 123 x 69 x 160 mm
4) LC Pro* | 2017 | 23.8”- 3840 × 2160 px | 470 x 240 x 340 mm
5) LC HR2* | 2018 | 9.7”- 2048 x 1536 px | 196 x 147 x 250 mm
6) LC Precision 1.5 * | 2018 | 5.5″- 2560 x 1440 px** | 121 x 68 x 160 mm
7) LC Magna | 2019 | 23.8″- 3840 x 2160 px** | 510 x 280 x 350 mm
8) LC Dental* | 2020 | 14″- 3840 x 2160 px** | 310 x 174 x 200 mm
9) LC Opus* | 2021 | 14″- 3840 x 2160 px** | 310 x 174 x 220 mm
10) LC Titan | 2024 | 32″- 8K 7680 x 4320 px** | 695 x 385 x 1200 mm
11) JENI | TBC | CConfigurable based on requirements | Configurable (w)
x 800 (d) x 2440 (h) mm
*Printer no longer on sale
**Backlit screen technology introduced