Bohanna Art Case Study
Art Sculpters
Pierre Bohanna has a long and prosperous career in prop and Costume making, with an extensive list of blockbuster films he has worked on, including the Harry Potter and Star Wars franchises, The Dark Knight, Gladiator 2, Barbie, Dune: Part Two and many more. Throughout his captivating career, he has continuously expanded on his expertise and utilisation of different artistic and production techniques and tools, including adoption of additive manufacturing solutions through the use of Photocentric LCD 3D printers and services.
Outside of the prop making world lives Bohanna Art, where Pierre has transferred his knowledge and experience in prop making, to meticulously craft sculptures and art pieces, with the assistance of his two in-house LC Magna 3D printers
Pierre Bohanna Interview
The man behind the art
What was your introduction to additive manufacturing and rapid prototyping?
Pierre – “My history is in film prop making and specialised costume making. I’ve always by nature of the job, looked for novelty. When I’m working on a film, I try to provide for the productions, a capacity and diversity for how we make things.
Everything is about wanting to see interesting and novel things. With that principle in mind, the first time I really started using rapid prototyping was at the beginning of production for the Harry Potter films. I purchased a small third party 6” machine and was able to make props like the compass for The Golden Compass film. This was a great introduction to 3D Printing – probably the most problematic, faulty piece of equipment I’ve ever had, but it was a great learning curve which opened us to the possibilities of 3D Printing.”
What persuaded you to purchase two LC Magna printers?
Pierre – “Initially I was attracted to them because I like resin machines, there’s good dexterity in the different products you can put into it, so it’s not just one thing. Also the LC Magna is a good sized machine, but also the fact that Photocentric is responsible, you look after us very well, and you’re two hours up the road rather than on the other side of the world.
Being pro-British manufacturing is a cornerstone for us. We have a consistent relationship with our supply companies, especially those involved with casting and moulding. We don’t just buy something and never make contact again, so Photocentric being answerable and contactable has enabled an ongoing relationship.”
Has the LC Magna enabled you to diversify in what you offer?
Pierre – “Yeah, we’re proof of that. We bought LC Magna to facilitating what we already did (prop making), but in the following three years we’ve expanded our capacity and how we interpret the LC Magna’s capabilities massively and Bohanna Art is a result of that.
Both of our LC Magna machines are in use all the time, they’re a very busy part of what we do. Bohanna Art is a combination of that route of really looking for non-film based businesses that can really utilise the skills of what we have internally and apply the equipment to it. It makes our work really individual, which is a cornerstone principle of Bohanna Art.”
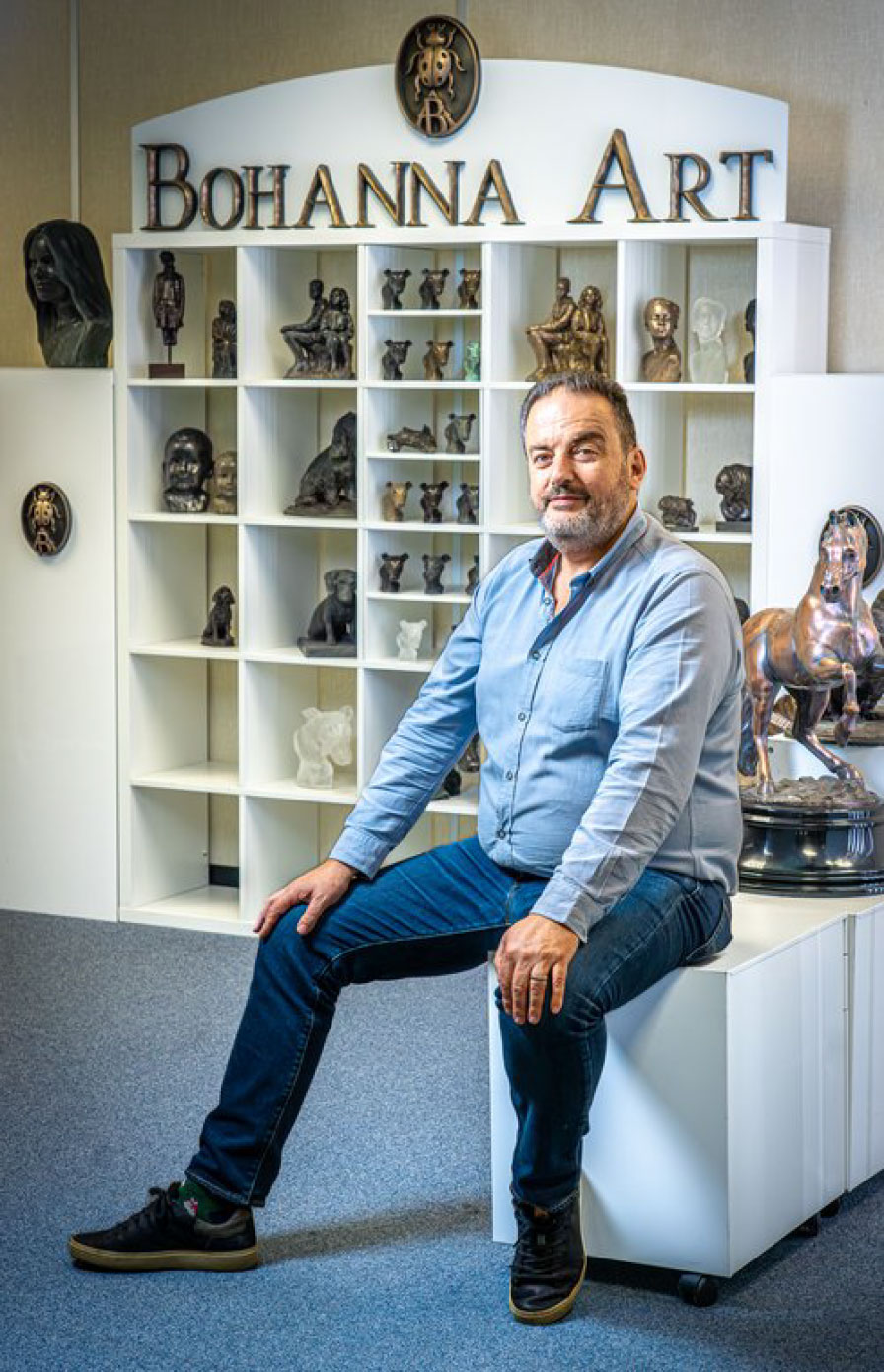
Bohanna Art makes some truly beautiful art pieces, utilising indirect production methods. What does the overall production process look like for you?
Pierre – “Let’s use Rufous as an example. We brought in lovely Rufous and scanned him, with all of his beautiful portions and shapes, his lumps and bumps.
The 3D digital model then goes to our digital sculptor, who takes the raw data and re-stylises the file. We think of it as how a sculpture would classically do it, it’s not just a cut and paste process. There’s sculpting tool marks, softening, work on the eyes, and a lot of sculpting techniques that are involved to make it work. We try to bring an authentic, handmade feel to the work that’s being done.
We then take that information, prep it and grow it on the LC Magna. We like to think of the 3D printing as growing, it’s an old habit, it’s like if you’re growing tomatoes and someone asks, ‘have you grown that yet?’. Once it’s been grown and post cured, there’s hard finishing and proprietary work that’s then carried out to the print. This is called the hard pattern.
The pattern then gets moulded. We tend to use the method of block moulding, as it is a very efficient way of doing it. Once ready we then cast the prop or part. Once it comes out of the mould, we do all the finishing work, including various patination techniques. Then it is boxed and sent to the client.
The pattern can be reused to create multiple moulds. Occasionally, whilst it is being moulded, you have to break it up to remove it from the mould, if it’s a very complicated shape. So it can have preconceived break lines and be grown with the understanding that it will be sacrificial pattern. But, because of having the LC Magna in- house, that’s not a problem, because we can just grow another one. It’s all dependent on what we’re doing, and the LC Magna allows us to be flexible.”
What are some of your art ventures that having the LC Magna has enabled you to explore?
Pierre – “We made a 3D version of Henri Rousseau’s Tigers in a Tropical Storm (Surprised!) which was all pattern work done on the two LC Magna machines we have in-house. I believe the piece contains over 300 patterns, nearly every blade of grass eventually became different pieces, because they needed to be individually created. All of that work was done utilising the LC Magnas. It was like, ‘We’ve got Magnas, what can we do with them?’ That was a classic example of me walking into the National Gallery with the head of retail developer wondering what can we do to make some really impressive pieces, which we called aspirational pieces. As I was walking around, I looked at Rousseau’s painting and thought, ‘that would be amazing in 3D’. I can do that because I know I’ve got the confidence in the process and the LC Magnas.
Every individual piece of that 3D artwork was individually cast, and it wouldn’t have been possible without incorporating the LC Magna into that process. That piece was a year of work. If we were trying to make it 20 to 30 years ago, you’d have had to have physically sculpt it. It would perhaps take three or four times the amount of time to produce, which basically makes it impossible; I don’t think that piece would be possible practically unless you had all the time in the world and significant funding/investment. It just shows you what is possible by applying the processes of the LC Magna.”
What are some of your art ventures that having the LC Magna has enabled you to explore?
Pierre – “We made a 3D version of Henri Rousseau’s Tigers in a Tropical Storm (Surprised!) which was all pattern work done on the two LC Magna machines we have in-house. I believe the piece contains over 300 patterns, nearly every blade of grass eventually became different pieces, because they needed to be individually created. All of that work was done utilising the LC Magnas. It was like, ‘We’ve got Magnas, what can we do with them?’ That was a classic example of me walking into the National Gallery with the head of retail developer wondering what can we do to make some really impressive pieces, which we called aspirational pieces. As I was walking around, I looked at Rousseau’s painting and thought, ‘that would be amazing in 3D’. I can do that because I know I’ve got the confidence in the process and the LC Magnas.
Every individual piece of that 3D artwork was individually cast, and it wouldn’t have been possible without incorporating the LC Magna into that process. That piece was a year of work. If we were trying to make it 20 to 30 years ago, you’d have had to have physically sculpt it. It would perhaps take three or four times the amount of time to produce, which basically makes it impossible; I don’t think that piece would be possible practically unless you had all the time in the world and significant funding/investment. It just shows you what is possible by applying the processes of the LC Magna.”
How much of the Art on the Bohanna Art website was an LC Magna involved in the making of?
Pierre – “Everything on the Bohanna Art website has pretty much involved the LC Magna.”
What are some of your aspirations for future projects with Bohanna Art, and how do you see Photocentric machines enabling you to achieve them?
Pierre – “The chance to make full-sized pets using the LC Titan, that would be an interesting proposition.
I’d also love to do horses. My dream is to be able to have a horse run through our scanner so we can capture it in full movement, but also if a dog is jumping and catching a ball – that would be amazing. A pet is something that people are really proud of, and an LC Titan enables us to have the option of giving people a life size pet sculpture.”
Printing Solutions for Arts & Entertainment
Photocentric LCD 3D Printers offer scalable, high-quality prototyping and production capabilities for a wide range of creative industries, with cutting-edge resolution and production efficiency.
LC Titan
Massive Build, Precision at Scale
Unlock the power of very large-scale production with the largest LCD 3D printer in the world. Featuring a massive build volume and 8k resolution, it’s designed for high-volume production with exceptional precision.
LC Magna
Versatile Medium-Sized Printing & Prototyping
Ideal for medium-scale prototyping and production, offering efficient production and 4k resolution. Perfectly complements LC Titan in a full workflow for seamless prototyping and production capability.