Capacité d'impression par jour
Pièces imprimées par équipe de 8 heures avec 20 x Liquid Crystal Magnas
Merit3D, une entreprise leader dans le domaine de la fabrication additive, produit 1 000 000 de cintres pour Adhesives Technology en utilisant la technologie de l'impression 3D. Les cintres sont nécessaires pour chaque projet entrepris par Adhesives', mais le processus de production a été interrompu en raison de l'indisponibilité de l'outil de moulage par injection.
La solution de Merit3D a permis à Adhesives Technology d'éliminer les coûts supplémentaires et le temps d'attente pour la livraison d'un nouvel outil et de ramener la fabrication aux États-Unis.
Processus de conception en 3D
2 semaines - itérations multiples pour optimiser les coûts et les performances
Imprimante 3D
20 x Photocentric Liquid Crystal Magna
Matériau
BASF ForwardAM
Résine Ultracur3D® EPD1006
Suspensions par plate-forme
400
Temps d'impression par plate-forme
225 minutes
"Il s'agit d'une étape importante dans le développement de la fabrication pour remplacer le moulage par injection, car nous voyons de grandes entreprises remplacer leurs processus de fabrication actuels par des pièces issues de la fabrication additive".
Le défi
Accès à l'outil de moulage par injection
Adhesives Technology a dû relever des défis en raison d'événements mondiaux empêchant l'accès à son outil de moulage par injection. Cet outil était nécessaire pour produire des supports permettant de maintenir ensemble les cartouches d'époxy et les buses de mélange. Le processus de production a été interrompu et la mise en place d'un autre outil aurait pris trop de temps, ce qui a fait de l'impression 3D la seule option viable. Toutefois, l'impression 3D des supports aurait été d'un coût prohibitif.
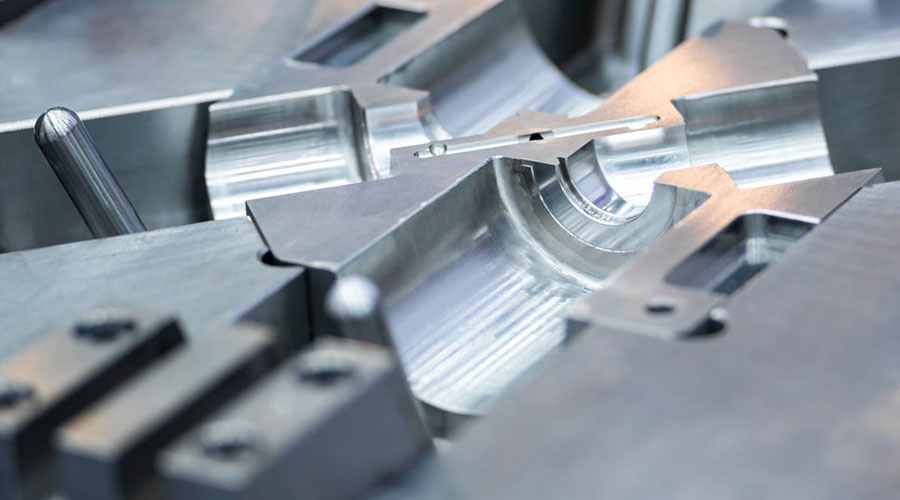
Solution
Liquid Crystal Magna
Merit3D a proposé une solution à ce défi en modifiant la conception du moulage et en l'optimisant pour la fabrication additive. Plus précisément, l'entreprise a optimisé la conception pour les imprimantes Magna de Photocentric's Liquid Crystal . Le processus itératif de reconception de Merit3D a duré au total deux semaines et a abouti à une conception qui pouvait être imprimée en 3D de manière efficace et rentable.
Merit3D a utilisé 20 imprimantes pour produire les cintres, avec 400 cintres par plateforme, ce qui a pris 225 minutes par plateforme. Le matériau utilisé était l'Ultracur3D® EPD1006 de Photocentric et BASF ForwardAM, qui présentait les propriétés idéales et a passé avec succès le test de durabilité brutal.
Élimination d'un outil de moulage par injection coûteux
Réduction des déchets et de l'empreinte carbone
La solution de fabrication additive de Merit3D a permis à Adhesives Technology de continuer à travailler avec la commande de 1 000 000 de cintres, éliminant ainsi le besoin d'un outil de moulage par injection coûteux. La solution de l'entreprise a également permis des personnalisations et de multiples itérations de conception afin d'optimiser les cintres pour leur utilisation spécifique. L'utilisation de la technologie de fabrication additive a également permis de réduire les déchets et l'empreinte carbone.
PhotocentricLes imprimantes Magna de Liquid Crystal se sont révélées idéales pour la fabrication en série en raison de leur grand format, de leur finition de surface élevée, de leur production rapide, de leurs résines rentables et fonctionnelles et de leur faible consommation d'énergie.
La production réussie de Merit3D de l'ordre de 1 000 000 de cintres à l'aide de la technologie de fabrication additive démontre le potentiel de cette technologie pour la production à grande échelle. En optimisant la conception pour l'impression 3D et en utilisant les imprimantes Magna Liquid Crystal de Photocentric, l'entreprise est en mesure de produire les cintres de manière efficace et rentable.
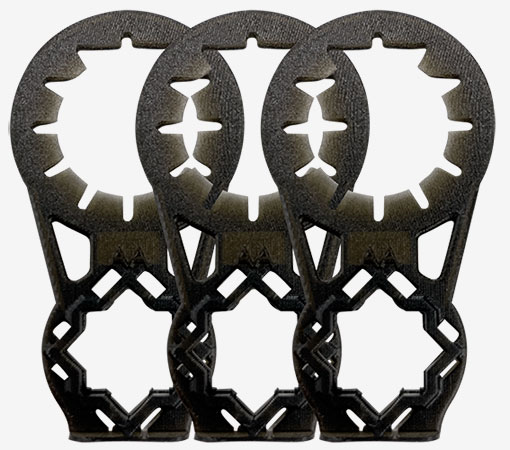
Capacité d'impression par jour
Pièces imprimées par équipe de 8 heures avec 20 x Liquid Crystal Magnas
Merit3D, une entreprise leader dans le domaine de la fabrication additive, produit 1 000 000 de cintres pour Adhesives Technology en utilisant la technologie de l'impression 3D. Les cintres sont nécessaires pour chaque projet entrepris par Adhesives', mais le processus de production a été interrompu en raison de l'indisponibilité de l'outil de moulage par injection.
La solution de Merit3D a permis à Adhesives Technology d'éliminer les coûts supplémentaires et le temps d'attente pour la livraison d'un nouvel outil et de ramener la fabrication aux États-Unis.
Processus de conception en 3D
2 semaines - itérations multiples pour optimiser les coûts et les performances
Imprimante 3D
20 x Photocentric Liquid Crystal Magna
Matériau
BASF ForwardAM
Résine Ultracur3D® EPD1006
Pièces par plate-forme
400
Temps d'impression
225 minutes
"Il s'agit d'une étape importante dans le développement de la fabrication pour remplacer le moulage par injection, car nous voyons de grandes entreprises remplacer leurs processus de fabrication actuels par des pièces issues de la fabrication additive".
Le défi
Accès à l'outil de moulage par injection
Adhesives Technology a dû relever des défis en raison d'événements mondiaux empêchant l'accès à son outil de moulage par injection. Cet outil était nécessaire pour produire des supports permettant de maintenir ensemble les cartouches d'époxy et les buses de mélange. Le processus de production a été interrompu et la mise en place d'un autre outil aurait pris trop de temps, ce qui a fait de l'impression 3D la seule option viable. Toutefois, l'impression 3D des supports aurait été d'un coût prohibitif.
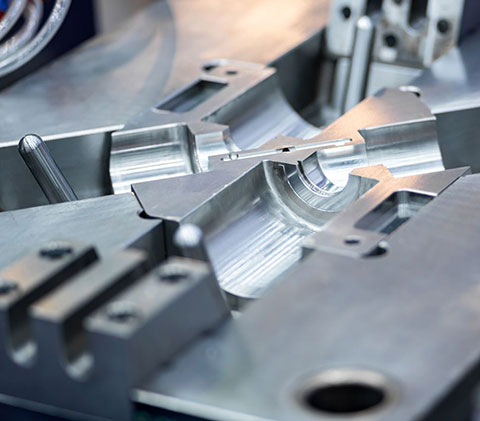
Solution
Liquid Crystal Magna
Merit3D a proposé une solution à ce défi en modifiant la conception du moulage et en l'optimisant pour la fabrication additive. Plus précisément, l'entreprise a optimisé la conception pour les imprimantes Magna de Photocentric's Liquid Crystal . Le processus itératif de reconception de Merit3D a duré au total deux semaines et a abouti à une conception qui pouvait être imprimée en 3D de manière efficace et rentable.
Merit3D a utilisé 20 imprimantes pour produire les cintres, avec 400 cintres par plateforme, ce qui a pris 225 minutes par plateforme. Le matériau utilisé était l'Ultracur3D® EPD1006 de Photocentric et BASF ForwardAM, qui présentait les propriétés idéales et a passé avec succès le test de durabilité brutal.
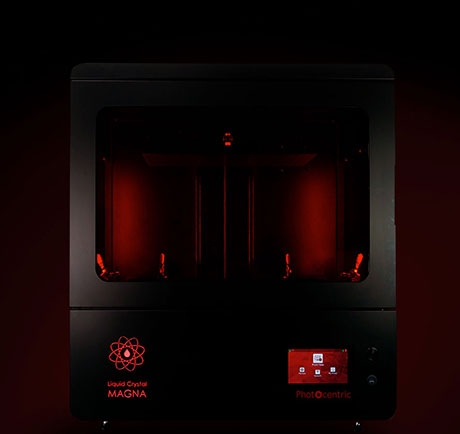
Élimination d'un outil de moulage par injection coûteux
Réduction des déchets et de l'empreinte carbone
La solution de fabrication additive de Merit3D a permis à Adhesives Technology de continuer à travailler avec la commande de 1 000 000 de cintres, éliminant ainsi le besoin d'un outil de moulage par injection coûteux. La solution de l'entreprise a également permis des personnalisations et de multiples itérations de conception afin d'optimiser les cintres pour leur utilisation spécifique. L'utilisation de la technologie de fabrication additive a également permis de réduire les déchets et l'empreinte carbone.
PhotocentricLes imprimantes Magna de Liquid Crystal se sont révélées idéales pour la fabrication en série en raison de leur grand format, de leur finition de surface élevée, de leur production rapide, de leurs résines rentables et fonctionnelles et de leur faible consommation d'énergie.
La production réussie de Merit3D de l'ordre de 1 000 000 de cintres à l'aide de la technologie de fabrication additive démontre le potentiel de cette technologie pour la production à grande échelle. En optimisant la conception pour l'impression 3D et en utilisant les imprimantes Magna Liquid Crystal de Photocentric, l'entreprise est en mesure de produire les cintres de manière efficace et rentable.
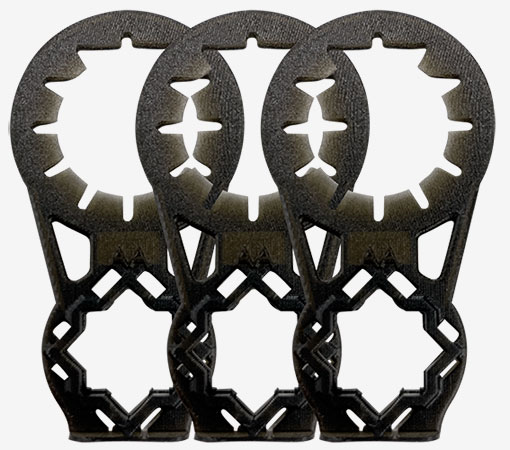
Découvrez d'autres études de cas