3D Printing – the smart choice for manufacturing from SMEs to large-scale manufacturers
In today’s fast-paced and competitive manufacturing landscape, the need for efficiency, flexibility, and cost-effectiveness has never been greater. Alongside traditional methods such as injection moulding, 3D printing has rapidly emerged and established itself as a transformative technology that is very capable of addressing these changing demands, offering businesses of all sizes a powerful and flexible production method.
With applications spanning prototyping, tooling, mould-making, and full-scale production, 3D printing offers both adaptability and precision, along with a range of other benefits to address the demands of modern manufacturing. In this article, we explore some of these benefits.
Prototyping: Fast Iteration and Functional Testing
One of the primary advantages of 3D printing is its ability to accelerate product development. Traditional prototyping methods can be both costly and time-consuming, with long lead times tied to the method of production including expensive tooling. 3D printing solutions like the LC Magna enable businesses to rapidly produce prototypes with functional resins tailored to specific mechanical and aesthetic needs. This allows for faster iteration and refinement, and that final products are optimised before they full production.
Companies like Wurtec, a manufacturer of elevator components, have embraced LCD 3D printing to streamline their prototyping process. By using LC Magna, Wurtec achieved significant reductions in development time, allowing for quicker testing and refinement of designs, ultimately speeding up their product-to-market timeline – reducing prototyping lead times by 8-24 weeks, depending on the complexity of the tool.
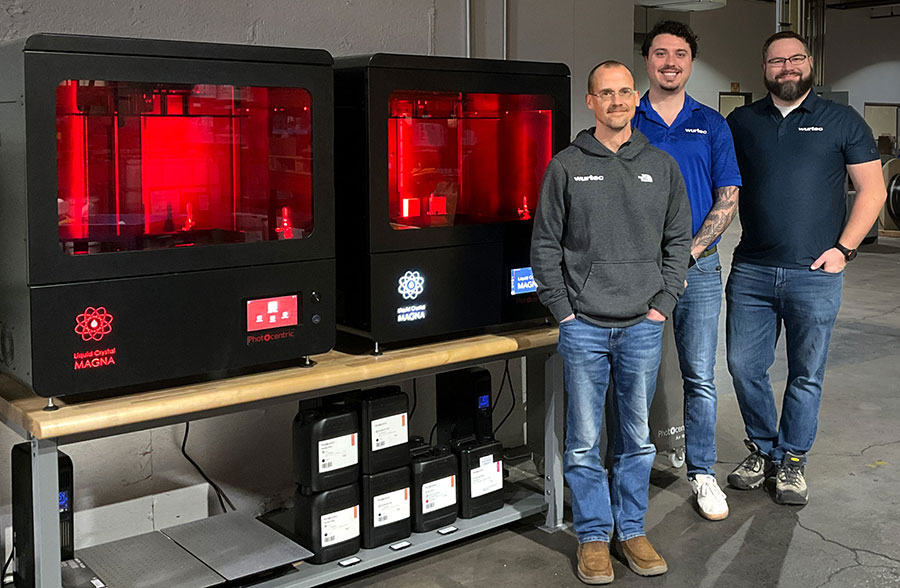
Wurtec Team with LC Magna’s
Tooling and Moulds: Reducing Costs and Lead Times
For manufacturers relying on traditional injection moulding, tooling is often one of the most expensive and time-intensive steps in production. 3D printing presents a compelling alternative, enabling the creation of complex, high-resolution moulds at a fraction of the cost and time. LC Titan and LC Magna are well positioned for industrial applications, capable of printing quality moulds with specialised resins that compete with traditional steel and aluminium tooling in terms of precision and durability. These technologies not only streamline the production process but also reduce dependency on external mould suppliers, enabling manufacturers greater control over their workflow.
Grisport, a manufacturer of high-performance footwear, has utilised LCD 3D printing to create accurate tooling and moulds, reducing both lead times and costs. The ability to iterate quickly and produce custom solutions has given Grisport a competitive edge in their respective market.
3D printed shoe mould
Many businesses have already seen the benefits of this approach. By integrating 3D printing into their production processes, manufacturers are eliminating delays associated with conventional tooling and reducing costs while maintaining the high quality and precision required for large-scale production.
End-Use Parts and Production Manufacturing
3D printing is no longer just limited to prototyping – it’s also increasingly being used for end-use production. With solutions like the LC Titan and LC Magna, manufacturers can produce high-quality, durable parts with precision and speed. These printers have made it easier for businesses to complete prototyping and move directly into producing custom components utilising the same 3D printing technology – something not possible with traditional injection moulding, with the additional benefits of reducing waste and eliminating long lead times typically associated with costly tooling/moulds.
Merit3D, an additive manufacturing company and Photocentric customer, partnered with Adhesives Technology, a leading manufacturer of high-performance adhesives, to produce a custom part used to secure epoxy cartridges and mixing nozzles. The original injection mould tool had become unavailable, threatening production timelines.
Merit3D confidently leveraged the capabilities of LCD 3D printing with LC Magna to rapidly design and produce 1,000,000 parts, at a capacity of 24,000 parts per day across their fleet of 20 LC Magna printers.
Merit3D parts in production
In a similar light, Photocentric’s production parts service has produced millions of end use parts to date for a wide range of customers globally. This has included printing 5 million face shield separators on 45 Magna printers (equating to 50,000 parts a day) and developing large complex automotive panels for Magna International on our largest printer, LC Titan.
Print Farm producing face Shield brackets
For small to medium enterprises (SMEs), making use of a production parts service via a contracted partner can offer a very cost-effective entry point into utilising 3D printing capabilities. Through outsourcing the production of parts to a print farm, SMEs can access production capability without the need for significant upfront investment in equipment, deploying or upskilling resources, offering a great point of entry into using 3D printing and avoiding the long lead times and additional up-front costs of traditional production methods.
Material Innovation: Functional and Specialised Resins
Beyond the hardware, LCD 3D printing offers an extensive range of photopolymer resins. These materials can be engineered to offer specific properties such as high strength, temperature resistance, flexibility, or biocompatibility. Unlike traditional manufacturing, where material selection can be restrictive and costly, 3D printing allows for a tailored approach to production, ensuring that each part meets the precise functional requirements of its intended application, with the added benefit of being able to easily switch between materials without much delay.
Range of 3D printed parts
The rise of automation and new opportunity for 3D printing in mass manufacturing
3D printing, particularly with solutions like the LC Titan and LC Magna, has already transformed manufacturing with its flexibility, precision, and cost-effectiveness. These technologies remain ideal for companies needing rapid prototyping and/or requiring low-mid production volumes, offering a scalable solution that’s both efficient and adaptable.
However, for large-scale manufacturers, the tide is turning. The latest innovation from Photocentric, JENI, the latest innovation from Photocentric, combines high-speed, high-volume production with unparalleled consistency, integrating material handling, printing, washing, and curing into a single automated platform. This makes it a game-changer for large-scale manufacturers – reducing waste, eliminating the need for large inventories, and significantly reducing overall cost and time to production when compared with traditional approaches such as injection moulding.
JENI – the first fully autonomous digital mass manufacturing platform
Similarly, for small to medium enterprises (SMEs), JENI can offer a very cost effective service based model, providing easy access to high-performance digital manufacturing without the need to invest in hardware. This on-demand solution reduces environmental impact and enhances design flexibility – all through a digital parts ordering solution – a new solution that Photocentric has developed in close partnership with the UK Smart Manufacturing Data Hub (SMDH).
This evolution in 3D printing and in particular for mass manufacturing, the advent of JENI as a disruptive technology that rivals the status quo of today’s solutions, offer businesses the flexibility to produce what they need, when they need it, all while reducing costs and waste. Whether you’re an SME needing to scale, or a large-scale manufacturer – 3D printing has something to offer today, and in the next generation of manufacturing.